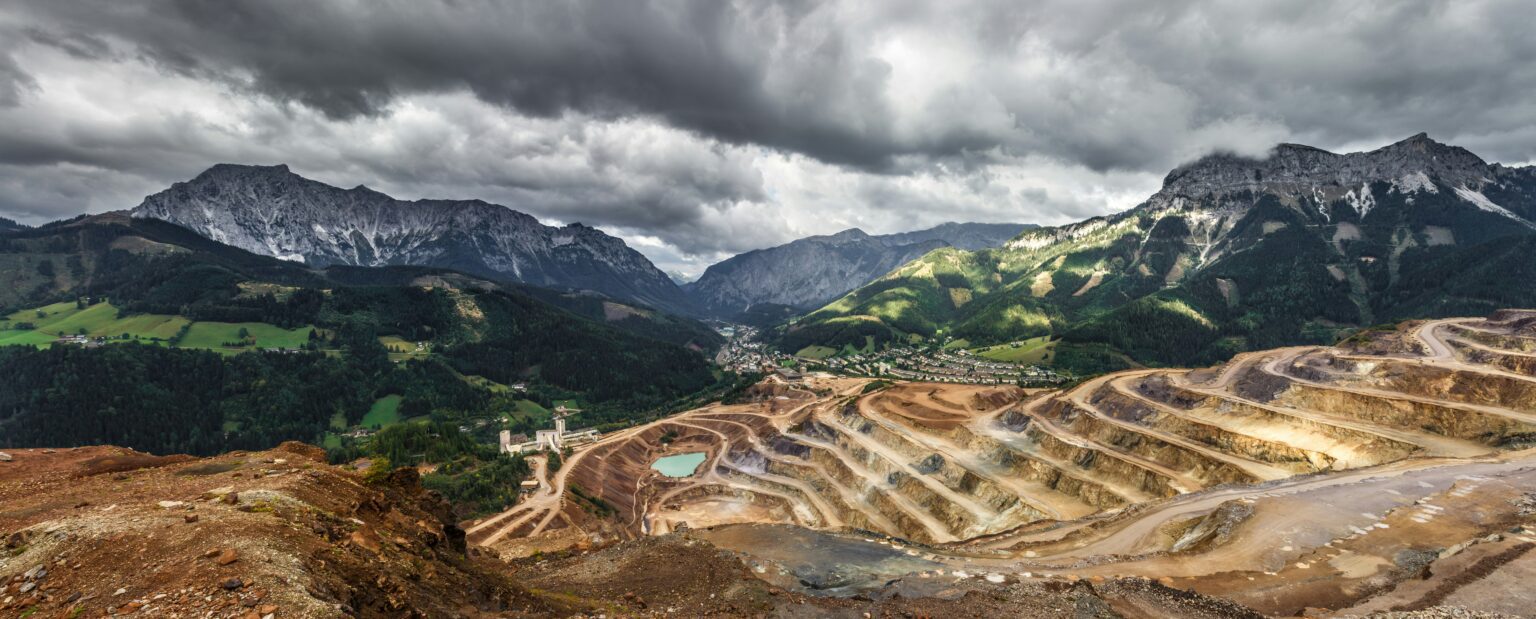
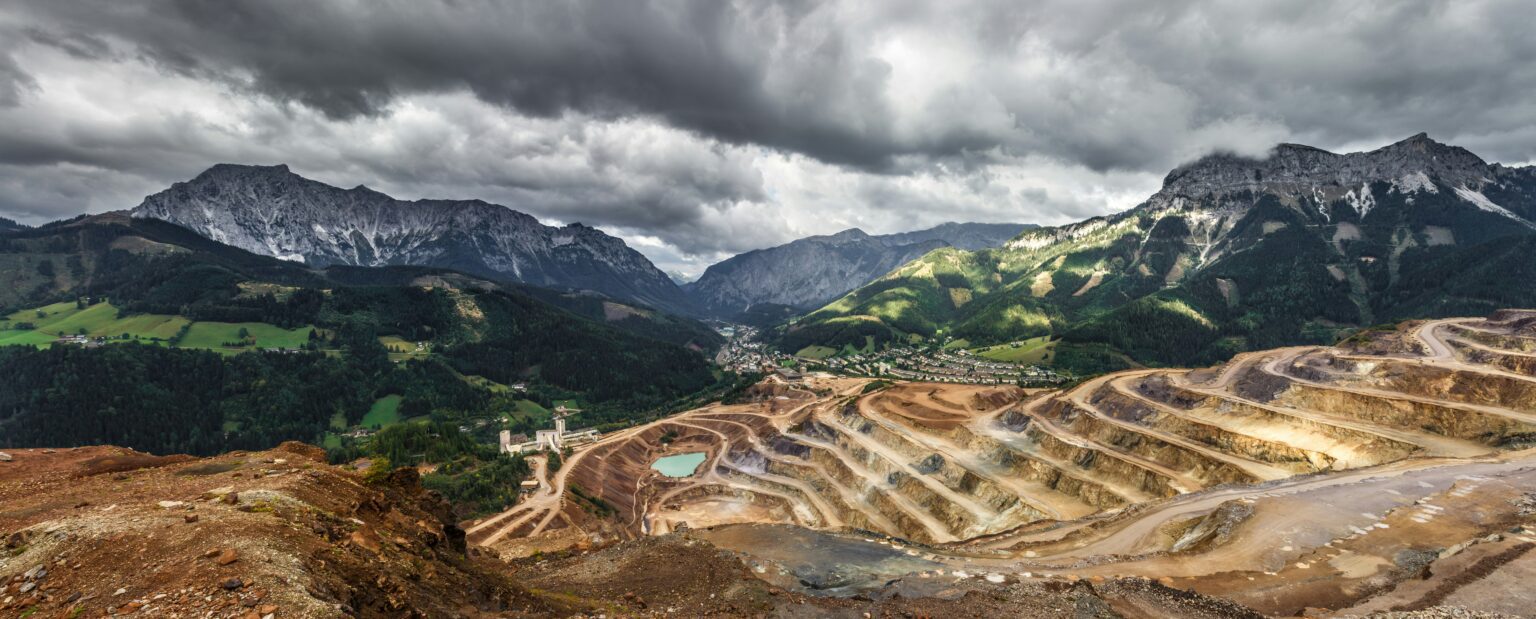
In the late 19th century, mining operations began to embrace electricity, seeking a more efficient and safer alternative to coal-powered steam engines. This early adoption of electric power transformed mines, bringing electric lights, machinery, and enhanced ventilation systems, creating a safer and more productive environment. However, as the 20th century progressed, the landscape of mining technology shifted dramatically.
The demand for greater mobility, flexibility, and efficiency led to the widespread adoption of diesel engines. These engines, with their high energy density and reliable power, became indispensable, especially in remote mining locations far from electrical grids. Post-World War II, the established diesel fuel infrastructure and its cost-effectiveness cemented diesel’s dominance. Diesel engines offered superior power and operational range, robustness in harsh mining environments, and lower initial and operational costs compared to the early electric alternatives.
Fast forward to the modern era, where technological advancements and the mounting pressure to reduce carbon emissions have reignited interest in electrification. Although cable-tied electric vehicles (EVs) have been used for the past 50 years, the real game-changer has been the development of battery-operated mining machines, culminating in the development of Australia’s first prototype battery system designed for a zero emission mining haul trucks. This momentum has been enabled by rapid improvement in the battery energy density, resulting from global investment in decarbonisation.
Today, the market boasts battery-electric haul trucks, drills, explosives, conveyors, and light towers. Despite this progress, diesel-powered vehicles still accounted for 46% of a mine’s total energy consumption in 2021, presenting a significant challenge with their undesirable environmental characteristics. This reversion back to electric is driven by the need for sustainable and efficient energy solutions, marking a new chapter in the evolution of mining technology.
This article will examine the rise of modern electrification, the catalysts which have spurred recent progress and the challenges which still lie ahead when it comes to achieving full electrification.
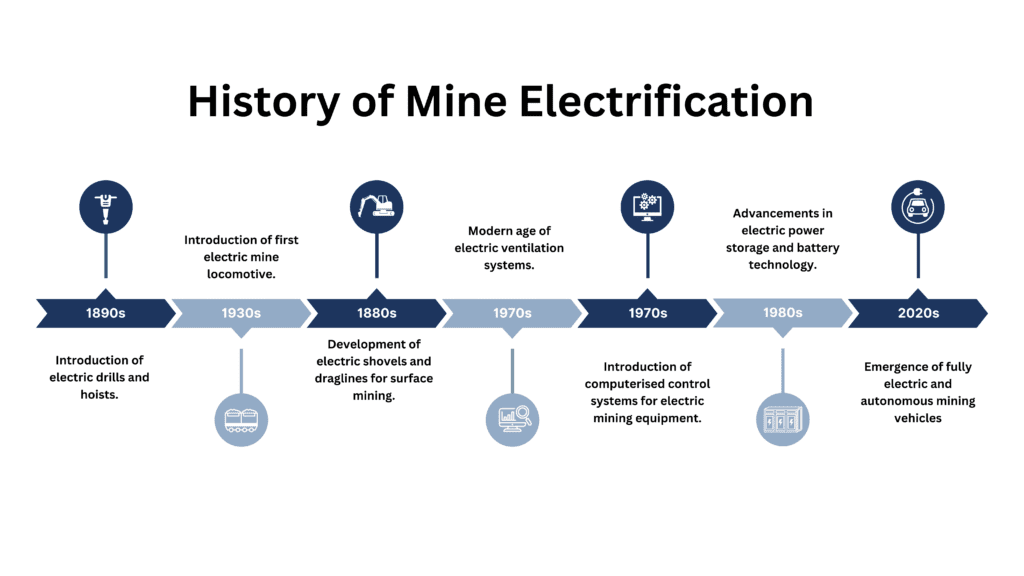
Figure 1. Evolution of Electricity in Mining Technology and Processes
The Rise of Modern Electrification
The recent shift towards electrification has been largely driven by advancements in technology. Central to this transformation is the evolution of battery technology. Enhancements in energy density, charging speeds, and battery longevity have made electric mining vehicles and machinery more viable than ever. This leap in technology reduces operational downtime and maintenance costs, making electric alternatives not just a sustainable choice, but also an economically sensible one.
A compelling example of this progress is evident in the decline in lithium-ion battery prices over the past decade. From US $780 per kilowatt-hour (kWh) in 2013, prices have plummeted to US $139 per kWh by 2023. This 82% reduction, as illustrated in the accompanying chart, reflects significant technological advancements and economies of scale.
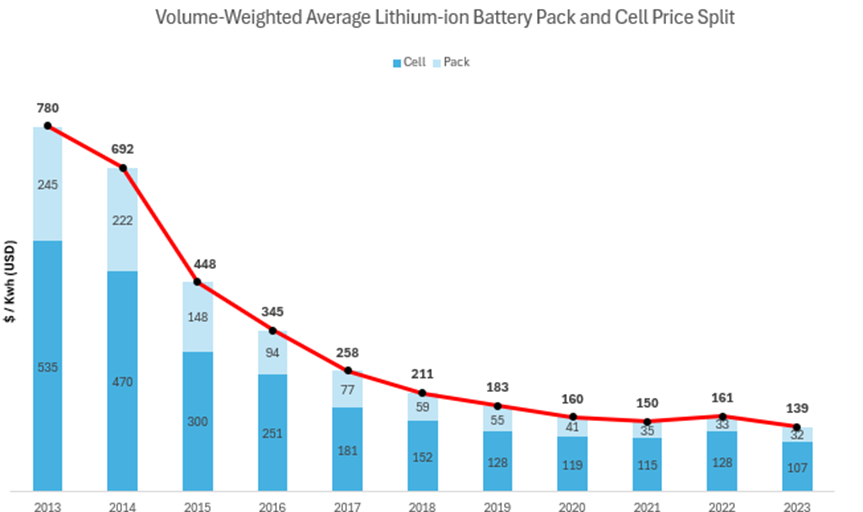
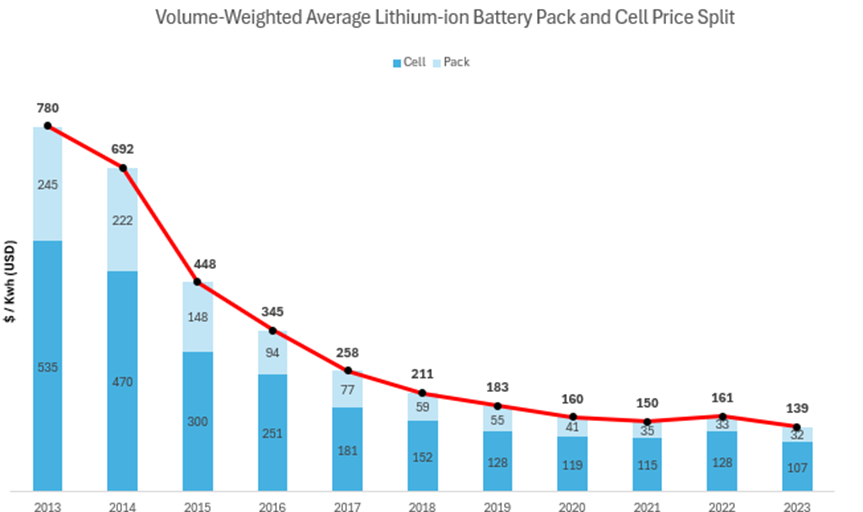
Figure 2. Source: BloombergNEF
Battery technology isn’t the only area experiencing rapid progress. Charging technology is also evolving, with innovations aimed at minimising downtime. Ultra-fast charging stations and wireless charging solutions, like by ABB’s eMine™ FastCharge, promise to keep electric mining vehicles operating continuously with minimal interruptions.
Moreover, the cost of electric mining equipment is becoming more competitive. Companies like Caterpillar and Sandvik are leading the charge with their electric and autonomous machinery. Although electric vehicles (EVs) are characterised by higher capital hurdles, their long-term benefits in terms of fuel savings and reduced maintenance are undeniable. A recent report has stated that electrifying a single 150 Tonne Diesel Truck usually requiring over US $850,000 per year in fuel, can save mining companies US $5.5 million in energy costs per vehicle over its lifetime.
Despite progress, challenges remain with battery technology. Battery capacity imposes range limitations on battery-operated haulage vehicles, presenting challenges for mines reliant on long incline truck hauls. Although some mine designs are more favourable for battery electric vehicle (BEV) truck haulage, deep decline-centric haulage designs are currently less suitable. Additional batteries also introduce inherent hazards including thermal run-away leading to fire or explosion, fume generation during a fire and ruptures causing toxic or flammable liquid/gas release.
Another critical factor in this electrification journey is the development of robust electric infrastructure. Reliable energy storage and distribution systems are essential, especially in remote mining locations where consistent power supply is a challenge. Advances in grid technologies and microgrids are making it possible to integrate renewable energy sources, further enhancing the sustainability of mining operations. These systems ensure that even the most isolated mines can benefit from the reliability and efficiency of electric power. These advancements do not come without their challenges – implementing charging infrastructure in electrified mines can be costly and disruptive, especially for brownfield projects where retrofitting existing layouts are challenging. Additionally, optimising battery swapping to ensure availability and manage battery health and lifecycle requires precise coordination, impacting overall efficiency.
Navigating Market Volatility: Impacts on Mine Electrification
Despite investments and advancements in new technology, progress in mine electrification is still dependent on a range of unpredictable factors.
One of these factors is the price of key battery minerals, particularly lithium. Recent years have seen significant fluctuations in the global lithium market due to the advancements in the development and demand of EVs. Within a two-year period lithium carbonate prices shifted from a low of US $5,850/t in July 2020, to a high of US $79,650/t in 2022, reflecting shifts in supply and demand dynamics.
Such volatility and confusion around price can also be seen in future projections from financial institutions. In April 2024, major broker Citi recommended shorting the CME August 2024 lithium hydroxide futures contract, anticipating a decline of US$6700/t, and doubled down on this short recommendation again in the month following. This decision was based on a reset in global EV sales expectations and a significant market surplus of about 6% of total supply. Citi also predicted that lithium prices would drop below US$12,000/t over a six-to-nine-month period, which could rebalance the market. These expectations are in stark contrast to the price highs of 2022.
The short-term bearish outlook on lithium prices may present challenges for mine electrification. Lower prices may discourage investment in new lithium mining projects, particularly from junior miners who might struggle to secure funding. This could lead to future supply constraints just as the demand for lithium for mine electrification rises. Electrification of mines, which relies on a stable and affordable supply of lithium for batteries, could face delays or increased costs if supply becomes restricted. A compelling example can be seen more recently, where the collapsing lithium price has pushed miners to cut costs and scale back expansions following the recent fall of lithium carbonate prices.
Pilbara Minerals, an Australian spodumene producer, experienced a 46% revenue drop in the December quarter due to low and volatile lithium prices, pressuring high-cost producers. This trend is evident across the industry, with Core Lithium Ltd. halting operations at the Grants open pit to address market oversupply, and IGO Ltd. adjusting the offtake pricing model for the Greenbushes mine and planning production cuts in the second half of the year.
China’s Role in Shaping Mine Electrification
The story of mine electrification would not be complete without acknowledging China’s pivotal role. As a dominant force in the supply chain of critical battery minerals such as lithium, cobalt, and nickel, China wields considerable influence over future technological advancements and market pricing.
China plays a key role in the global supply of critical minerals essential for mine electrification. The country is set to increase its share over the global cobalt market, with its portion of global production expected to reach half of global output, up from 44% currently. Its dominance in chemical refining for battery production is even more pronounced, accounting for a 77% of global refining capacity. The nation’s influence further extends to rare earth elements, where it produces 60% of the world’s supply but processes nearly 90% of it. This dominance allows China to exert significant influence over the global supply chain, impacting the availability and pricing of critical minerals necessary for the transition to electric mining operations. This dominance highlights the importance for other nations to consider their supply chains and invest in domestic capabilities to mitigate risks and ensure continuous innovation in mine electrification.
Beyond raw materials, China’s impact is evident in the manufacturing of electric mining equipment and infrastructure. The nation is a leading producer of EVs and battery technologies, benefiting from economies of scale, low labour costs and advanced manufacturing capabilities. Chinese manufacturers, such as BYD Company, as well as Contemporary Amperex Technology Co. Limited (CATL) not only supply domestic demand but also export to global markets, driving down costs and making electrification projects more economically viable. As a result, the capital costs of electrification infrastructure and equipment are influenced by Chinese production capabilities and pricing strategies.
The Path Forward
As the mining industry faces increasing pressure to decarbonise, companies are confronted with the challenge of balancing sustainability goals with economic realities. Market volatility of important battery minerals and technology, as well as geopolitical factors, further complicate this landscape, forcing many to prioritise immediate financial performance over long-term environmental targets. We have recently seen BHP announce the closure of its Nickel West division in Western Australia, which produced 80,000 tons of nickel annually and employed over 3,000 people. This decision came in response to a collapse in nickel prices and increased competition from Indonesian producers. BHP’s decision to shut down its Kalgoorlie smelter, Mt Keith and Leinster mines, and Kwinana refinery highlights the economic pressures and operational challenges faced by the industry.
Amid these challenges, the role of innovation and strategic collaboration cannot be overstated. Engaging in pilot projects, conducting regular market analysis, and forming strategic partnerships with technology providers and other stakeholders allow companies to test innovations, gather essential data, and distribute risks. By leveraging these strategies, mining companies can navigate the complexities of electrification while remaining agile and competitive in an ever-evolving industry.