Mine Electrification: An Industry Mindset Shift
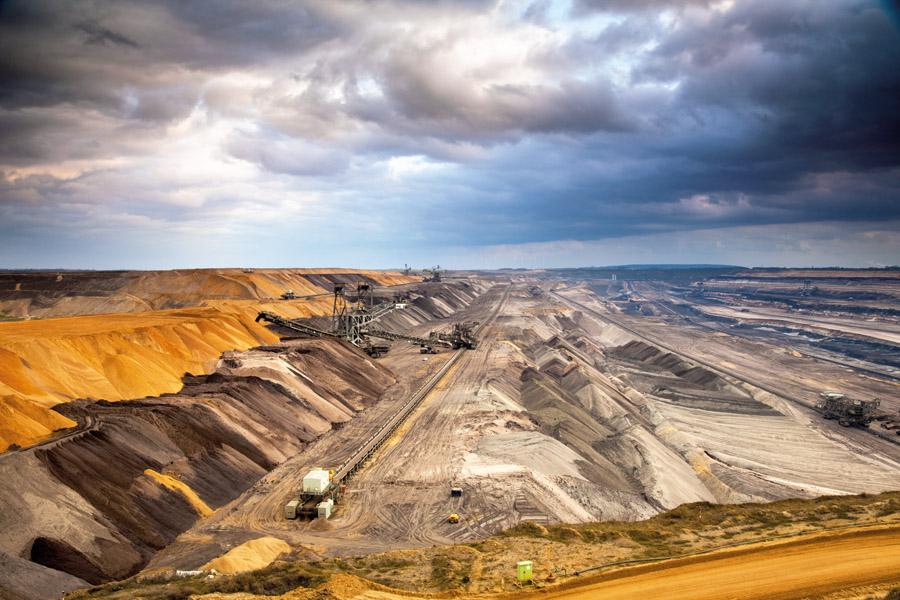
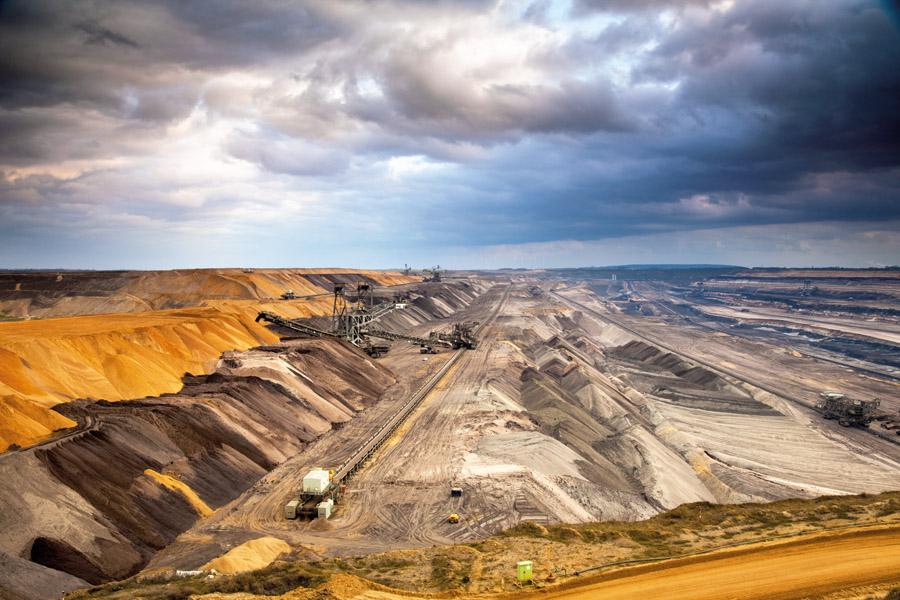
This article was written for the 2023 Industrial Net Zero Conference.
The shift from a fossil fuel powered mine to an all-electric mine will require more than just a shift in the technology required. It requires a mindset shift by the broader industry. The predisposition to continue with what is comfortable, simply replicating existing asset design processes, is no longer viable as we think about 2030 and beyond. This will challenge an industry that traditionally has little risk appetite when it comes to mine design. In the 2021 State of Play Mining Industry Survey, only 20% of mining businesses stated they would accept risk in asset design to increase financial return. An all-electric mine requires a refresh in thinking about design across the entire value chain, and many traditional mine design principles will need to be set aside.
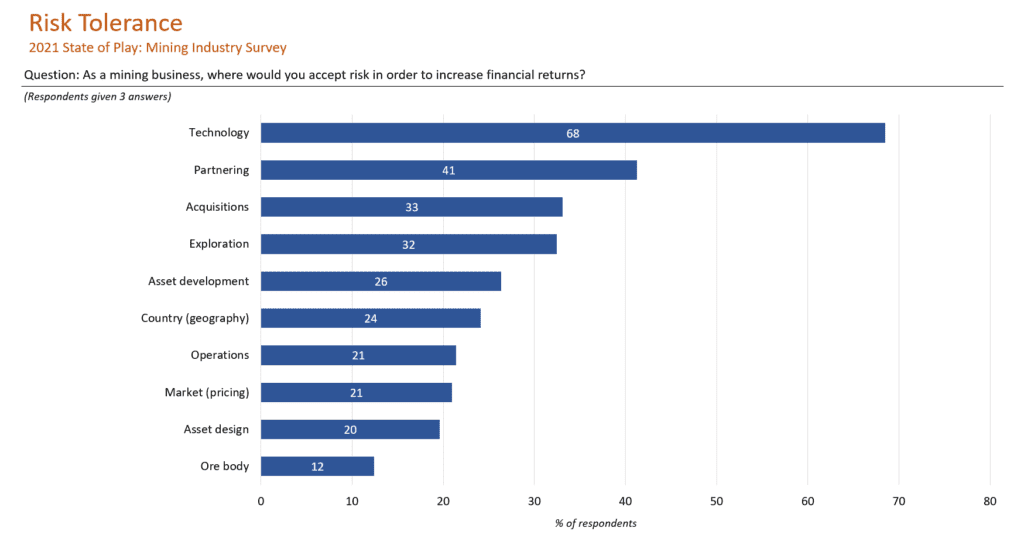
So, if we want to capitalise on this shift and embrace emerging technologies, what do we need to consider in the mine design process?
Equipment
While there are battery electric vehicle solutions available today, technology is still evolving. In designing an all-electric mine, not only must the fleet size and composition be considered, so must the ability for equipment solutions to adapt. Optionality will become critical to embed in decision making processes for equipment, allowing companies to adopt to the emergence of new technologies with minimum disruption. Battery swapping, for example, is currently used in some electric vehicles. While this may be the best fit for certain mine sites now, for many it is seen as inefficient as it is capital intensive, and operations are interrupted to make the swap. Embedding optionality in fleet selection provides the opportunity for process efficiencies to be capitalised on as breakthrough technologies emerge.
Ventilation
Using battery electric vehicles generally results in a decrease in required air volumes, which likely means building smaller, and potentially fewer, ventilation shafts. An all-electric mine not only creates benefits for worker health and safety (an electric fleet will reduce heat emissions by up to 90% and eradicates diesel particulate matter) but may also result in significant cost and efficiency savings. Given that ventilation can use up to 50% of a mine’s electricity, the economic benefit of reduced ventilation operating costs could be significant. The ability to design mines with smaller ventilation infrastructure from the outset will also reduce capital costs.
Mine layout and infrastructure
In the State of Play Electrification report, 54% of mining companies expected infrastructure to be the main challenge for transitioning mine sites to electric. This is not surprising when you consider the needs of battery electric vehicles. Charging type, location, size of charging bays, feasibility of onboard charging, shift scheduling and optimal material movement are critical considerations for all mining companies.
Mine layout of electrical infrastructure will be key to optimising efficiencies. The strategic placement of charging stations will be important, as the timing and location of charging impacts how much energy is required and where at any given time. Optimising material movement can also impact energy efficiencies. By designing a mine that optimises haulage routes, there is the potential to capture energy from regenerative braking. While other infrastructure, such as trolley assist systems, need to be fixed, it is possible to capitalise on the charging opportunities from the overhead power bar system.
Processing design
Shifting to an all-electric mine requires a shift in thinking around processing design and efficiency. Where an all diesel mine can be planned around 24/7 processing, an all-electric mine needs to ideally accommodate fluctuations in renewable energy. To accommodate this shift, one of two changes must be implemented. Either processing remains 24/7 and is supplemented by renewables stored in a long duration energy storage solution, or processing design must fundamentally change, allowing flexibility to ramp up processing during the day when there is proliferation of solar or wind energy. Minimal processing would occur at night, resulting in the need to ‘stockpile’ during the day.
The mine design process will continue to evolve as new technologies are developed. It is critical however, that we question the rule book of traditional mine design and consider new approaches to accommodate the future needs of electrification. We should not underestimate the mindset shift required to meet this challenge.