State of Play: Ecosystem – Low footprint mining innovation
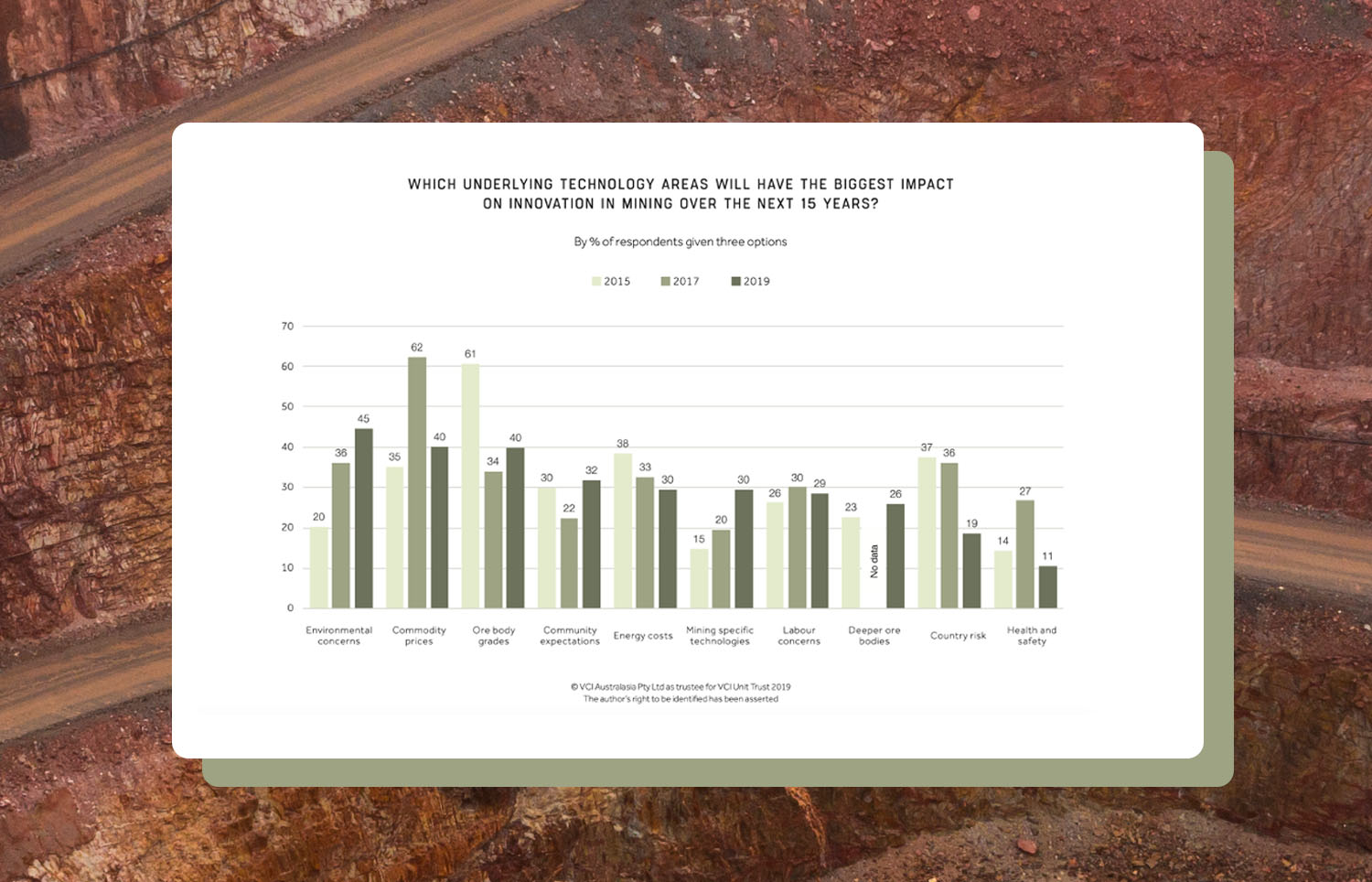
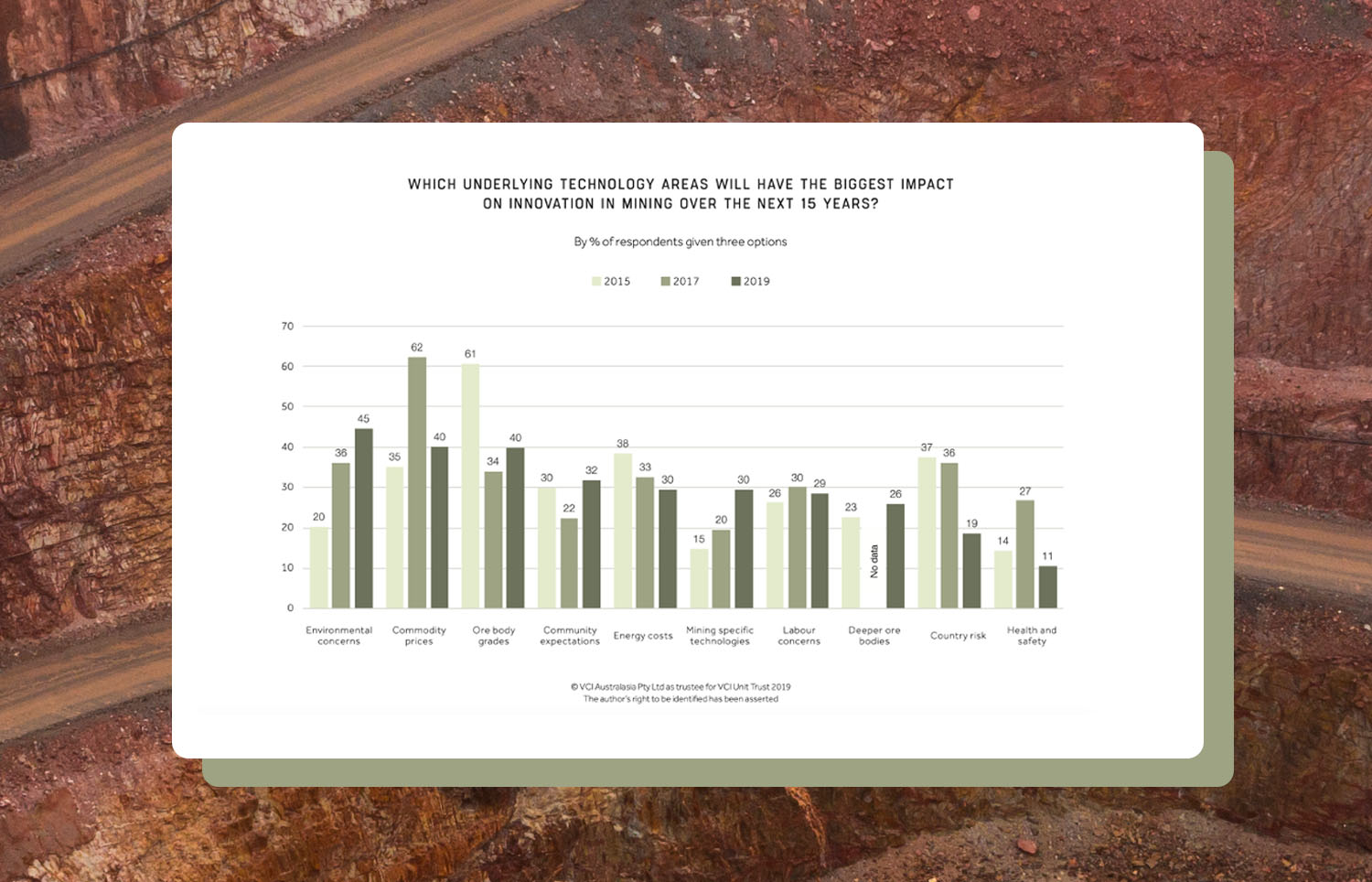
Local communities are less tolerant of large-scale disturbance on their land, new electrification technology is increasing possibilities of underground processing and transformational mining techniques are rapidly changing mining operation possibilities.
“We are seeing a change in climactic conditions whereby over the next 5-10-20 years, we will be forced to change the way that we design our projects and the technology we use.”
Low-footprint extraction is being achieved through precision extraction and processing technologies, which ultimately save significant energy. In-situ extraction uses chemical leaching to remove valuable ore while leaving minimal disturbance. Optimising the chemical mix leads to potentially significant returns, as does a potential shift to bioleaching.
Organisations such as Mining3 are developing other low-footprint methods in particular in-line and in-mine mining techniques. In-line mining uses technology to shift processing underground “to the face” to reduce the movement of waste material and the operational footprint above ground. In-mine mining uses refrigerants to build a wall around an orebody and avoid contamination when subsequently leaching the ore. Each of these potential methods promise to increase the precision with which miners extract ore as well as reducing footprint. Given that 80% of total operating costs are related to energy, low-footprint techniques that provide a step-change reduction in energy offers significant economic benefits.
Precision extraction technologies are further enabled by low-emission energy sources; new water sources; low-impact inputs through supply chain transparency; recycling; and rehabilitation. This section discusses the broader ecosystem implications of these changes.
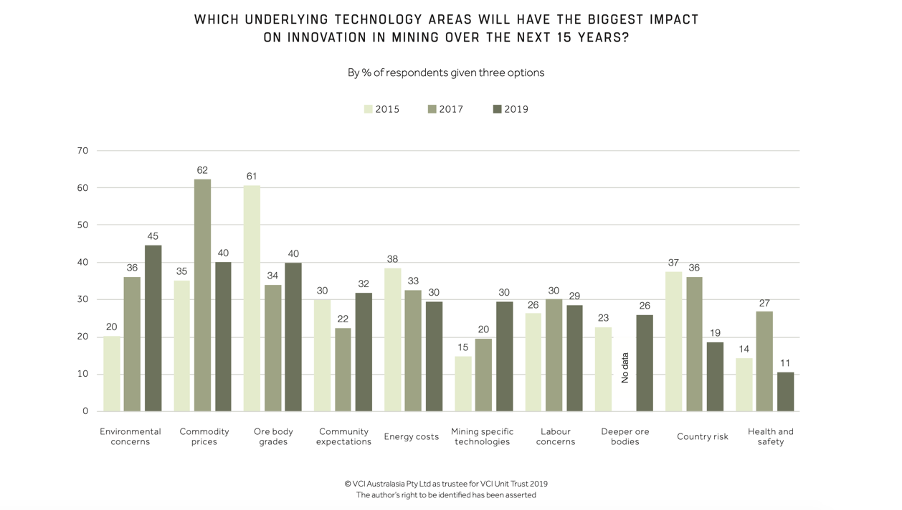
Coming full circle
The mining industry is the first stage of every global value chain. If end products themselves don’t include minerals mined around the world, their production systems certainly do. This cements the industry’s place in the global economy, yet the potential for a shift towards closed loop production systems, is undercutting base demand for some commodities.
As recycling methods improve and social consciousness drives people to recycle more goods, the availability of substitutes to virgin materials will continue to increase. The capital stock in China increases, scrap steel and other recycling is growing as well – Chinese domestic scrap steel production grew by almost half to 18% of total steel production (101 mtpa) in one year following a 2017 government directive. Smaller electronic goods are also increasingly being built to be recycled, beginning to close the loop for manufacturers such as Apple and Samsung, with a specific focus on aluminium and rare earth metals. This puts competitive pressure on the industry, especially consumer technology-facing industries such as battery minerals and aluminium.
We have seen this before; US steel company Nucor reimagined the steel supply chain based on the use of recycling scrap steel through the adoption of Electric Arc Furnaces and thin strip casting technology to become the largest and most successful steel producer in the US. In addition, Volkswagen are currently investing in lithium recovery capabilities for lithium-ion batteries, which may disrupt the demand profile of a nascent lithium mining industry. Whether this will this happen in other commodities remains an open question.
The most precious resource
The global mining industry is a prolific user and mover of water. Miners use water to transport ore and waste, mine and process ore, cool and clean equipment and rehabilitate mines. This adds up; for instance, over 250 megalitres of water is required to produce a tonne of gold. Mining companies also relocate huge volumes of freshwater though dewatering procedures necessary to enable safe mining access.
In addition, the mining industry seems to struggle with handling water safely. The failure rate of tailings dams over the past 100 years is 1.2% compared to a rate of 0.01% for other water storage dams. This is driving innovation in three areas:
- Reduction in the overall use of new water. Recycled wastewater and seawater is increasingly employed by miners such as Newcrest and Antofagasta.
- Reduction in the impact of operations on the water reserves. Miners such as Rio Tinto and Anglo American recycle water used on operations back into their operations or into local water supplies.
- New processes that require less or no water. As wet tailings dams increasingly become unviable, dry processing methods continues to face significant innovation focus.
Current approaches to using water in mining is likely to be untenable going forward. We see a future where water comes from recycled sources and is limited in use. We expect significant technical innovation to remove tailings dams from current operations, and new processing methods to remove the need for them going forward.
Turning back the clock
Despite its inevitability, mining companies have historically not effectively planned for the decommission and rehabilitation of mine sites around the world. Upon decommission, mines often transition from care and maintenance into eventual disuse without much effort taken to rehabilitate the land. The effect of this is that there are now an estimated 560,000 non-rehabilitated mines in the United States alone.
Driven by technological transparency, there is increasing global pressure on miners to improve the extent to which old mines are rehabilitated. Local communities are more empowered to demand rehabilitation of old mine sites, and governments are listening. The increased profile of poor rehabilitation history in the mining industry threatens the viability of future projects.
Social pressure is driving a shift in thinking regarding mine planning and rehabilitation options in two ways:
- Miners are engaging in concurrent clean-up efforts while maintaining operations. With sophisticated scheduling and management, operators are able to use current cashflow (especially in high-price environments) to offset future liabilities.
- Miners are investing in low-footprint technologies to reduce end-of-liabilities through structural changes in extraction and processing methods.
Fundamentally, this is a business model question and is likely to become an increasingly important one. Becoming a leader in rehabilitation may begin to form a unique competitive advantage, especially in securing rights to mine in environmentally and socially sensitive places. Much of the innovation in this space is likely to be outsourced to services companies.